FAQs
What are the factors affecting the construction quality of Emery wear-resistant floor?
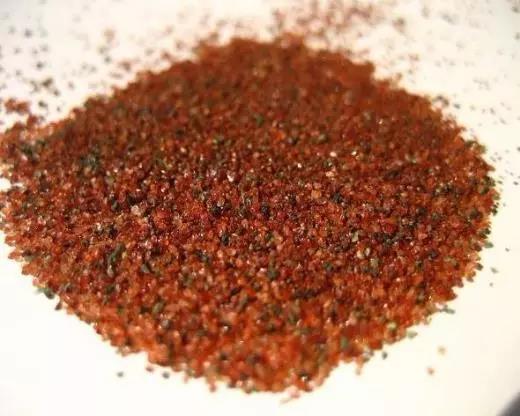
Everyone knows that Emery wear-resistant floor can withstand a certain weight, can also create different colors, can repair the entire ground tunnel, and durable, wear-resistant, dust-proof, easy to clean, etc., how to control the corundum The quality of the wear-resistant floor makes the above advantages more obvious. The lack of quality control will affect the overall quality acceptance criteria of the wear-resistant floor.
Today, we will bring you three elements to control the construction of emery sand-resistant floor. Today we will comprehensively explain the three elements of quality control of diamond wear floor.
The first element: controlling the color and quality of Emery wear-resistant floor
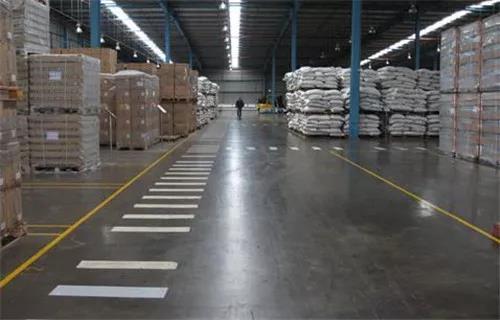
Ensure that the wear-resistant material and the cement concrete base layer are well bonded and the color of the floor is the same, mainly to control the timing of the wear-resistant material and the amount of spreading per square meter. The timing of the spreading should be selected in the initial setting stage of the concrete, the amount of spreading per square meter. The spreading should be achieved by spreading twice.
The second element: controlling the flatness of the surface of the wear-resistant floor of Emery
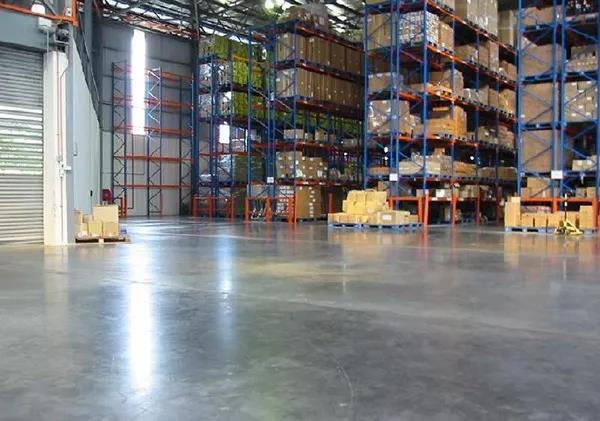
The flatness of the floor construction is mainly controlled by the flatness of the cement concrete base. The wear-resistant material is only a dense layer with a very thin surface, so it is especially important to control the flatness of the surface before the initial setting of the concrete. To strictly control the flatness of cement concrete pouring, it can be leveled by two times before and after.
In addition, in the construction joint adjacent to the two concretes, the trowel is not easy to be sanded when the floor is light-receiving due to the approach to the construction joint formwork, so the height difference is likely to occur at the construction joint. Therefore, the construction joint cleaning work should be carried out after the formwork is removed. The method is to cut the concrete of 50 mm width and depth about 50 mm along the construction seam elastic line with a cutting machine, and cut it off before the second pouring concrete, thereby ensuring that the concrete poured twice and the concrete that has been poured are flattened. Straight, pay attention to the line and cut should be straight.
The third element: preventing the occurrence of shrinkage cracks in the wear-resistant floor of Emery
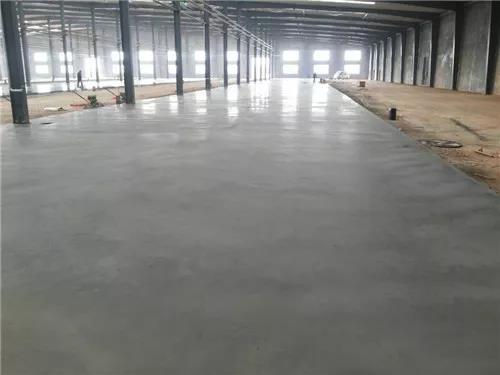
1. Control the dryness of the concrete surface before spreading the wear-resistant material. If there is water on the concrete surface, it must be cleaned and then spread, otherwise the water-storing part is prone to dry shrinkage cracks;
2, timely cutting expansion joints, after 2 days of cement concrete pouring, that is, the wear-resistant floor is completed 1-2 days after the completion of cutting, and then not function.
Recent post
contact us
Contact Person